How Does a Metal Disintegration Machine Work?
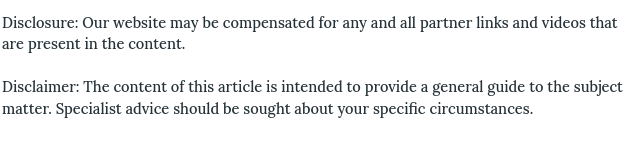
In the world of metalworking, various machines contribute to the manipulation and alteration of metals to suit specific needs. Among these is the metal disintegration machine (MDM), an essential tool for precise metal removal and machining. This article explores the intricacies of how a metal disintegration machine functions and addresses common queries surrounding its operation and application.
What is a Metal Disintegration Machine and its Purpose?
Understanding Metal Disintegration
Metal disintegration involves the process of breaking down metal components without affecting the surrounding structure. The metal disintegration machine is specifically designed to target and remove metal parts accurately. Its primary purpose is to disintegrate materials such as bolts, studs, and taps that are lodged within machinery without causing damage to the intact portions.
The technology behind metal disintegration prioritizes precision and efficiency. It ensures that only obsolete or broken parts of the metal are targeted, thereby preserving working components. This targeted removal is especially valuable in industries such as aerospace, automotive, and manufacturing, where machine integrity is paramount.
In applications where repair or salvage is necessary, metal disintegration machines provide a unique advantage. Their ability to accurately remove problematic elements saves time and costs associated with complete disassembly or replacement. This accelerates maintenance schedules and maintains the integrity of larger mechanical assemblies.
Components of a Metal Disintegration Machine
A metal disintegration machine is composed of several critical components. These include an electrode for disintegration, a power supply to control the energy input, and a cooling system to manage thermal loads during operation. Each component plays a vital role in ensuring that the machine performs effectively and efficiently.
The electrode is the primary tool used to erode the metal, and its composition varies based on the type of material being removed. The power supply modulates the energy, allowing operators to fine-tune the process according to specific needs. A reliable cooling system prevents overheating, ensuring continuous operation without disruptions.
Operators depend on these intricate components to achieve the desired metal removal outcomes. Regular maintenance of these parts is crucial to avoid operational downtimes. Ensuring that each component functions optimally allows the entire machine to operate smoothly and extend its service life.
Applications in Industry
Metal disintegration machines find extensive use in industries that demand precision and reliability. In the aerospace sector, they assist in the removal of fasteners and components that are otherwise challenging to access. This capability helps maintain the structural integrity of aircraft where precision is non-negotiable.
In the automotive industry, metal disintegration machines aid in the repair and refurbishment of engines and transmissions. They allow for easy extraction and replacement of worn-out parts, enhancing vehicle performance and lifespan. Such applications underscore the machine’s role in sustaining operational efficiency and cost-effectiveness.
How Does a Metal Disintegration Machine Operate?
Basic Operating Principles
The operation of a metal disintegration machine hinges on precise, controlled energy delivery to disintegrate metal. The machine directs electrical currents through an electrode, concentrating heat on the metal’s surface. This process breaks down the metal component without impacting the surrounding area.
Technical accuracy is crucial for achieving desired results, and operators rely on adjustable power settings. By modulating these settings, the machine can be adapted to various metal types and thicknesses, ensuring efficiency. Additionally, the machine’s design minimizes the need for further machining or finishing after disintegration.
The targeted removal facilitated by the machine enhances workflow in environments where precision machining is vital. This capability is advantageous in specialist industries that require exacting standards. The machine’s technological sophistication makes it an indispensable tool in the metalworking field.
Safety Measures and Best Practices
Ensuring operator safety is essential when using a metal disintegration machine. Proper training is crucial to understand and mitigate potential hazards associated with its use. Operators must follow industry-standard practices to maintain a safe working environment.
Protective gear, such as gloves and goggles, is recommended to shield users from metal shavings and electrical hazards. Regular safety audits and checks are vital to uphold safety standards and prevent accidents. Establishing a culture of safety ensures that operations continue smoothly without compromising worker welfare.
Metal disintegration machines play a crucial role in the precise and effective removal of metals across various industries. Understanding their operation and maintenance not only enhances productivity but also promotes safety. As technology advances, the evolution of these machines continues to contribute significantly to metalworking processes.
.